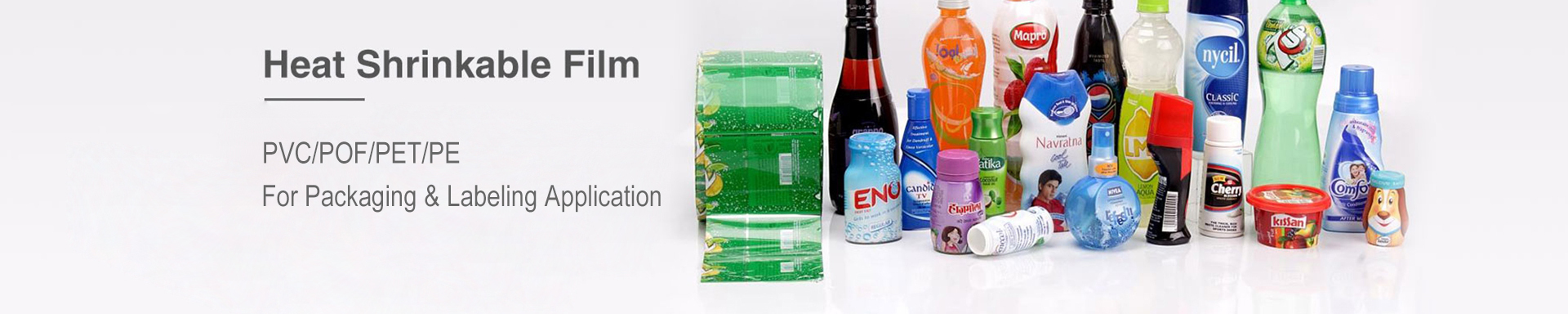
PE protective film plays a key role in the aluminum industry
2025-02-24 15:38Depending on the surface and film pressure, the viscosity rises at different rates, and it is generally necessary to leave the protective film for a sufficient period of time before peeling off to determine whether the viscosity is appropriate. For a certain surface, it is extremely important to choose the appropriate colloid and sticky PE protective film, and the subsequent processing steps are the key to determine the viscosity, and the subsequent processing generally includes cutting, bending, drilling, stamping, etc.
Generally, low-viscosity protective film is used for smooth surfaces, such as mechanical polishing and chemical polishing aluminum; Medium-adhesive PE protective film is used for medium rough surfaces, such as anodizing coloring, electrophoretic painting, chemical coloring, fluorocarbon spraying, and smooth electrostatic powder spraying aluminum; Very rough surface is made of high-viscosity PE film, such as electrostatic powder sandblasted aluminum; If laser cutting is required, the protective film shrinks when exposed to heat, so it is necessary to use a protective film with extra high viscosity. In addition to viscosity, users also need to test the tensile strength and elongation of the protective film to ensure that the flexibility and strength of the protective film can meet the requirements for use.